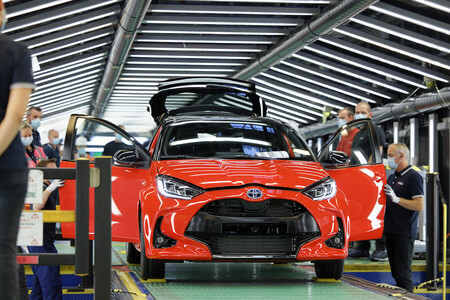
El coche que acabas de ver circulando por la carretera lleva cientos de horas de trabajo detrás para que todo ruede a la perfección. ¿Cómo puede un boceto sobre el papel convertirse en una potente máquina de conducción? El factor tecnológico y el humano se unen desde el brainstorm inicial hasta su presentación en sociedad para ofrecer la mayor calidad.
En Japón saben muy bien cómo alcanzar la perfección en el trabajo y así es cómo lo hacen. Vamos a sumergirnos en la fabricación de un vehículo japonés.
Papel y lápiz: donde empieza la inspiración
Una hoja en blanco y un lápiz es todo lo que necesita el diseñador para crear el prototipo de automóvil. La inspiración y la creatividad se dan la mano en esta etapa inicial donde se bosquejan los trazos que formarán la estética del vehículo.
En este punto, se debe valorar si se está comenzando un proyecto desde cero o si se trabaja sobre el diseño de su predecesor en una segunda generación. Estas cuestiones pueden ayudar a perfilar desde el mismo comienzo la mirada, el cuerpo y el impacto visual que va a tener el vehículo. Para Toyota hay dos conceptos que siempre deben estar presentes desde los primeros bocetos:
- Factor J: se refiere al gen japonés, la idea de conectar lo ancestral con lo innovador, la naturaleza y la modernidad y el compromiso con el medio ambiente.
- Vibrant Clarity: aquí entra en juego la lucha entre lo emocional y lo racional, enlazar lo creativo y lo práctico, lo atractivo y lo minimalista. El equilibrio debe estar claramente presente.
Una vez decidido, los trazos pasan a convertirse en avanzados diseños informáticos con herramientas y aplicaciones en tres dimensiones que dan una visión más efectiva del resultado final. Del bolígrafo al entorno virtual.
'Clay model', el concepto hecho realidad para asombrar
A continuación pasamos a obtener la primera versión material del diseño inicial. Un mock up a escala real y en arcilla (también conocido como clay model) que da una perspectiva en primera persona de cómo se distribuyen las proporciones y la sensación de espacio y accesibilidad de la cabina.
Estos modelos a escala 1:1 ya incluyen la pintura, ruedas, llantas y botonería interior y confieren una sensación visual del que será el coche final. Aunque aún el diseño es concebido únicamente como un prototipo, es en este punto en el que se observa cómo va a reaccionar el mercado ante su posible comercialización.
El concept car se pone a prueba en citas importantes como salones de automóviles, donde modelos como Setsuna, FCV o Ubox de Toyota han asombrado a propios y ajenos, a pesar de no haber pasado luego a fábrica. No olvidemos que la dificultad de este punto del proceso reside en que el producto ha de encajar en mercados tan variopintos como el asiático, el estadounidense o el europeo. No es fácil dar el salto definitivo a la producción.
Camino de la línea de estampación y soldadura
Comienza la fabricación tangible del vehículo. El trabajo de los robots con los sistemas de corte y soldadura transforma gigantescas planchas de acero o perfiles tubulares en los módulos que conformarán la estructura del coche: chasis, capó, puertas, salpicadero, portón del maletero, protecciones laterales, frontal, etc.
Antes de pintar, se aborda la fase de corte, soldadura y ensamblaje de los componentes del chasis
Las planchas de chapa son moldeadas a través de grandes prensas hidráulicas de hasta 8 metros de altura. A continuación, las piezas pasan a ser ensambladas mediante una soldadura eléctrica por puntos y remaches o adhesivos, realizada por los brazos robóticos.
Para ver en números el trabajo que hay detrás de la línea de estampación, podemos decir que un vehículo de gama media reúne alrededor de 3.000 componentes, los cuales a su vez tienen cientos de piezas.
Una vez montada la carrocería, ¡pasamos a la sección de pintura! Se lavan y eliminan los restos de grasa, se aplica una protección frente a la corrosión y se realiza un baño cataforético antes de empezar con las capas de imprimación.
Nos trasladamos a la cadena de montaje del equipamiento
Los motores se fabrican y montan en una sección específica y se llevan a la cadena de montaje junto a las cajas de cambio, las piezas de plástico, paragolpes, asientos, faros, neumáticos, frenos, salpicadero... Los operarios trabajan ensamblando todos los módulos en su carcasa de acero y conectan todas las piezas necesarias, desde soportes hasta tornillos y cableado.
Una vez instalado todo el equipamiento, el vehículo está listo y preparado para arrancar. Pero, antes de que llegue a las manos del usuario final, tiene que pasar por una inspección técnica.
El ojo perfeccionista del control de calidad
Un aspecto al que se presta especial atención en la fabricación de vehículos japoneses es al control de calidad. Pensaréis que se trata de un exceso de perfeccionismo de la mentalidad nipona, pero la verdadera razón está en la ceniza y arena del monte Fuji y sus islas volcánicas. Hasta 30.000 veces comprueban los robots el correcto funcionamiento de las ventanillas para dispersar las imperfecciones que puedan haberse insertado durante el proceso de montaje y que provocan arañazos en el cristal.
Una meticulosa inspección corrobora que todos los componentes están en perfecto estado
También se comprueba con precisión la conexión de las luces, la resistencia del techo panorámico y el volumen del equipo de sonido. Igual que la correcta rodadura de los neumáticos, la fluidez en la dirección y la respuesta de los pedales ante acelerones y frenazos.
El ajuste de todas las puertas y capó y cualquier fallo detectado durante el proceso de calidad del coche es anotado en papel, puesto que gozan de validez judicial. Se acaba con una revisión meticulosa con el objetivo de eliminar cualquier huella de la carrocería.
Comercialización y lanzamiento
¡Todo listo para echar a rodar! Un proyecto que Toyota cuida con mimo y detalle en cada uno de sus modelos, incorporando métodos productivos casi artesanales. No en vano, en 2019 la marca japonesa fue el segundo mayor fabricante mundial de automóviles.
En la planta de Motomachi, se fabrican modelos tan novedosos como el Toyota Mirai, del cual –en sus inicios– solo se fabricaban tres unidades diarias. Es una filosofía de producción basada en tiradas limitadas para ajustarse a la realidad del mercado. El ritmo de producción en cadena aumenta a medida que alcanza el punto óptimo en la economía de escala.
Es entonces cuando el nuevo modelo de Toyota se embarca en un periplo por tierra, mar y aire que, tras un proceso largo y tedioso, acabamos por disfrutar en el concesionario.
Imágenes | Sala de Prensa de Toyota